Mercedes-Benz has been able to produce and sell long-range electric vehicles (EVs) quickly, dispelling myths that manufacturing EVs is difficult, expensive, and may lead to job losses. While the transition to EVs in the automotive industry has indeed caused concerns about massive job cuts, Mercedes-Benz US International CEO Michael Göbel has found that making them is not much different from assembling a gas-powered car.
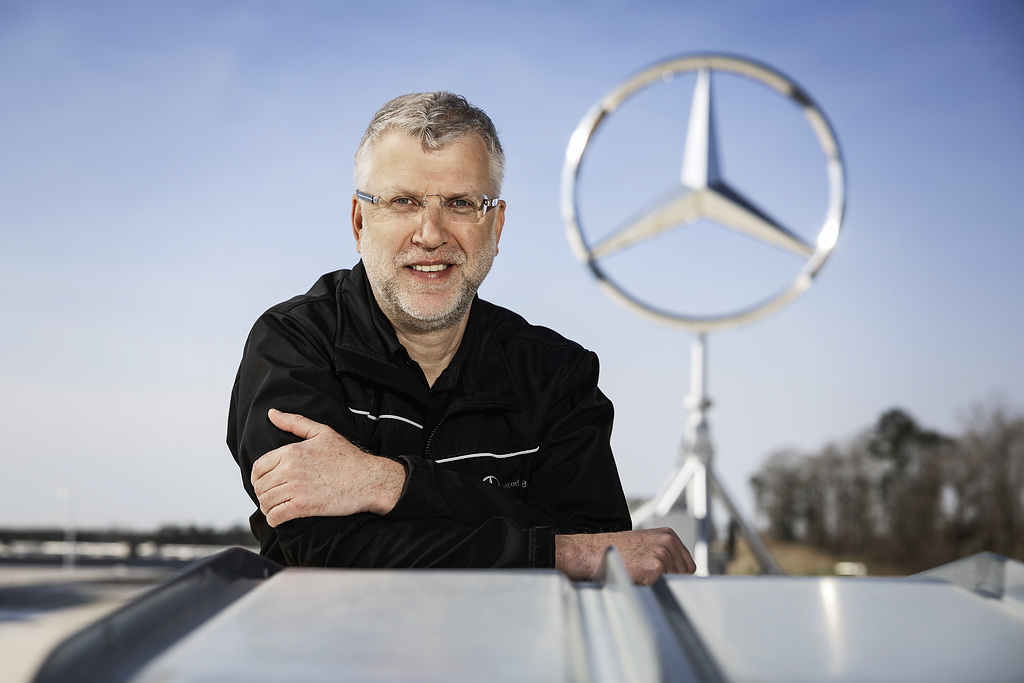
In an interview with Automotive News, Göbel explains that there is not a big difference in the build time of EVs and that the same processes are used in its basic assembly, such as screwing, clipping, or gluing. The main difference lies in the EV battery pack, which requires new “tolerances and accuracies”. However, with proper training and practice, it is possible to make them more efficient according to the exec.
The CEO admitted that while the efficiency of automotive manufacturing needs improvement, EVs could become less expensive if they are quicker and easier to assemble. He is bullish on the projection that the methods to make them would turn out to be cheaper and faster in about five to ten years from now.
Furthermore, Göbel said that the transition to EVs could create new job opportunities, such as dealing with battery cells, battery packs, software systems, and charging infrastructure. This is contrary to what the naysayers have been preaching about massive job cuts during the shift of automakers to EVs.
Thanks to Mercedes-Benz President Michael Göbel and team for hosting me at the Vance plant today, and for creating thousands of good jobs for Alabama. pic.twitter.com/kzwERuJpkm
— Coach Tommy Tuberville (@SenTuberville) April 5, 2023
Mercedes-Benz aims to have EVs make up half of its US sales by 2030 and has a goal to sell 45,000 EQ-branded electric vehicles in 2023. Initially skeptical about the demand for EVs in the past, Mercedes has eventually come to realize it underestimated customer support for electric cars and has turned its key focus towards it ever since.